Moon STEM 2025: Gator-Mouth LMF Models
- Jesse Quiroga
- May 30
- 5 min read
Scope of the Project
EAFab has a distinctive design for the Ladle Metallurgical Furnace (LMF), coined the "Gator-Mouth." In partnership with the local STEM program at Moon Township High School, six students came together to tackle a semester-long project. The project involves creating a miniature, fully functional, and modular model of our signature LMF to be used as a promotional item and display. Additionally, they were tasked to create an even smaller, mass-producible version of the model to be used as customer giveaways.
To reflect the expectations of a real-world assignment at EAFab, the students were given a limited budget and held responsible for material selection, transportation logistics, and fabrication planning.
The Journey
The project began with an introductory phase where students had to learn about what an LMF is, its function, and its role in the steelmaking process. Each student assumed responsibility for a specific part of the LMF and was accountable for its design and manufacture. Due to the interconnected nature of the "Gator Mouth" design, students had to use their communication and teamwork skills to work together and adapt to changes.

Most of the group’s time was spent on the design and engineering phase. Once each component's design met functional and aesthetic requirements, the STEM team transitioned to material sourcing and fabrication.
A range of processes was used, including 3D printing, CNC machining, and hand-finishing. The LMF body and skirts were primarily 3D printed, the top plate was fabricated from high-density polyethylene (HDPE), while the gantry, cart, and track were machined from cherry wood.
Part-by-Part Design and Manufacturing Process Overview
Roof Assembly: The roof was split into quarters to accommodate 3D printing and transportation constraints. After testing different strategies, the student found that angled joints provided better durability than flat ones and incorporated them into the design. Although time limitations prevented the roof sections from being fully glued together, the student recognized that doing so would have improved stability even further.

Top Plate: The top plate presented both technical strengths and setbacks. While the CNC programming was executed well, time constraints led the student to rush the sanding process, resulting in surface cracks and scratches. Although epoxy helped fix the damage, the experience taught the student the value of working meticulously and not cutting corners, rather than compromising on quality.
Gator Mouth and Fixed Skirts: The gator mouth was printed separately from its adjoining skirt. To keep everything aligned and prevent any damage during transport, the student added pins for a secure fit. The experience underscored how even small models need to be designed with mechanical stress in mind.
Ladle: The ladle design was revised multiple times to fit EAFab’s print bed and meet transportation requirements. The student then ran into a shortage of printing material, requiring him to re-split the ladle into more parts, and add more seams to the final product. This taught him the importance of planning ahead for materials and staying adaptable when problems arise.

Cart: Originally planned for 3D printing, the cart was ultimately machined from cherry wood due to its strength and simplicity. This shift introduced this student to CNC machining and the basics of structural design. Key takeaways included learning to create basic CNC code, understanding wood’s structural advantages, and valuing simplicity over over-engineering.
Track: Also made with cherry wood, the track was split in half and connected by magnets. This decision was made for ease of transportation. Because the track is thin and fragile, building it required precision and patience. The student learned the benefit of allowing enough time for careful work, planning for revisions, and following a step-by-step process to ensure accuracy when using power tools.
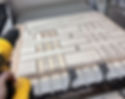
Gantry: The gantry component required CNC machining, gluing, screwing, sanding, spray painting, and use of a lathe. Early errors in CNC programming led to misaligned holes and electrode tapers not fitting as intended. Despite the setbacks, the student picked up a lot of hands-on experience, including how to use a lathe, countersink holes, and program CNC equipment independently. A memorable lesson, shared with humor, was the headache-inducing consequence of inhaling paint fumes during spray painting, reminding everyone of the importance of taking safety precautions in manufacturing environments.
Final Solution
As the end of the semester approached, the STEM team realized that they would not have enough time to complete the project in full. They then decided to focus their efforts on producing the mini-models for customer giveaways and use their remaining time to fabricate feasible parts.

This decision to recognize their limitations and adjust course does not undermine their work or efforts, but rather demonstrates accountability and adaptability—two skills that are very important and applicable to any career in any industry. Because of this pivot, the students successfully delivered a series of mini-models that retain the key visual and structural elements of EAFab’s signature “Gator Mouth” LMF. They were engineered to double as a small storage container for any small items or accessories that can't be safely worn into a steel mill, such as a wedding ring!
The team openly acknowledged the key reasons they were unable to finish:
Underestimating the amount of work they had left
Not working with the sense of urgency needed
Undermining fabrication lead times
Unexpected scheduling issues, including 2-hour delays, AP tests, and senior events
If given more time, the team shared that they would have added embossed and/or laser-engraved logos, scaled down the model for portability, and implemented a functioning linear actuator to match the real LMF Gator Mouth design. This project not only deepened the STEM team’s technical competencies across multiple engineering and manufacturing methods but also emphasized the softer skills of planning, teamwork, and communication.
Lessons Learned
Time Management: With only 50-minute class periods, unexpected delays, and occasional student absences, the students quickly learned how critical early planning is and to build in extra time for the unexpected. They also realized that lead times, whether for materials, equipment, or feedback, can make or break a project.
Communication: Clear and consistent communication, both within the student team and with EAFab, played a big role in keeping the project on track. The STEM team also adopted the mindset that “any idea is better than no idea,” which encouraged open brainstorming, creative problem-solving, and an environment where everyone’s voice mattered.
Among the other key takeaways were:
Prioritizing pre-planning and recognizing the over-engineering threshold
Valuing the prototyping and iteration stages
Researching and choosing the appropriate materials for each component
Understanding that simplicity often leads to more reliable and effective solutions
Appreciating the practical realities of fabrication
This project gave the Moon Township STEM team hands-on exposure to how complex, layered, and collaborative real-world work in the engineering field truly is. They not only created a viable solution that EAFab can continue to build on, but they also left the program with sharper technical skills, stronger soft skills, and a deeper understanding of what it takes to succeed in the workforce and further their careers.
